Have you ever heard of Digital twin ? Is it science fiction or a real strategic opportunity in the world of Industry 4.0 ? This article aims to introduce you to this new technology, which is brought in many sectors nowadays.
Digital twin, the future standard of Industry 4.0
Gartner defines the digital twin as « the digital model of a real process or object, made dynamic by the data that comes from that same process or object ».
It is therefore the digital representation (often in 3D) of a physical object throughout its life. This digital double appropriates all the components of its physical twin, as well as its properties. It is constantly fed with data, collected on its physical double.
The digital twin is therefore at the same time :
- the physical object
- its virtual representation
- the data generated
The added value of the digital twin lies in the analysis of the data collected by the physical object, opening the door to the predictive.
Let’s take the example of a storage tank : the sensors on the physical twin would bring the different data (temperature, pressure, flow, etc.) back to the digital twin. The analysis of this data will allow the engineers and technicians to spot malfunctions in real time but also to anticipate failures.
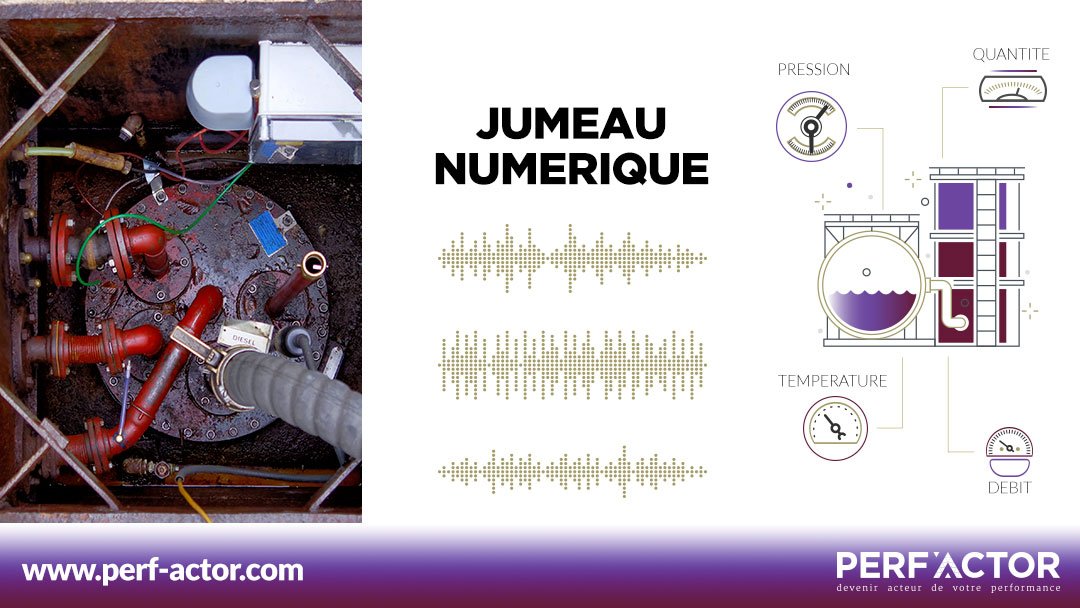
The solutions of digital twins are diverse and varied : abdominal aorta, airplane engine , smart citye or rail network.
There are many cases of use : IoT analytics lists 7 common uses and 252 possible combinations.

- multi-models
- multi-scales
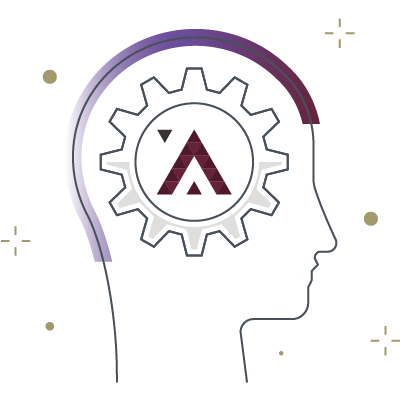
Feedback
From the view of the classifications, it is understandable that the business expectations of a digital twin will change overtime. We can imagine that the design phase will be accelerated when adding a new machine to an existing production line with a digital twin. This will be true provided that this digital twin is adapted to test and simulate the new manufacturing process and not just for preventive maintenance. The company will then be tempted to collect as much data as possible in the hope of handling all the cases. However, it is extremely difficult to predict what information will be relevant and therefore which sensors to install on the chain. The impact on costs will be enormous and the ability to make investments profitable will be seriously questioned. The company must prioritize the data to be collected and processed in order to focus on exploiting quality and controlled information. The maturity of the management of this data will change over time and the investments will be made with relevance and reason. Alexandre Langlais, CEO PERF’ACTOR« We can go a long way and make the corporate digital twins. The twin will then include very heterogeneous components: the machines, but also the production process, the human resources and even the financial constraints… », Michel Morvan explained, president of Cosmo Tech.Finally, they can possess artificial intelligence algorithms and machine learning tools that allow them to make decisions.
Predictive maintenance, interoperability and other benefits
The digital twin benefits from the synergies of the IoT, 3D design and predictiveness and has many advantages. Using data that have been collected and analyzed in real-time, the Digital Twin optimizes the design, the operation and the maintenance of an equipment and even an entire plant. By centralizing all technology data, this solution simplifies the access to documentation and facilitates the work of the technicians.
Unlike a physical object or a conventional simulation, the digital twin works continuously and provides information at all times about the current state of the system to which it is connected. But it also makes it possible to make real-time predictions about what will occur in the near future in terms of its current and past functioning.
Its role is also to enable different systems to communicate together and thus improve the interoperability. This involves developing a common language for defining twins and thus making it easier for integrators.
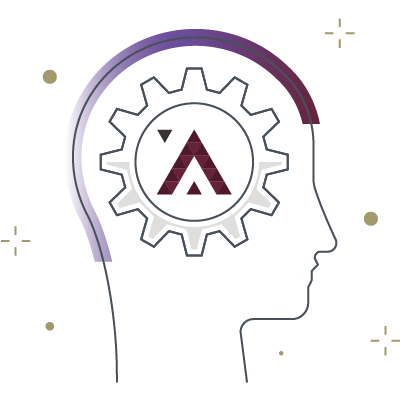
Feedback
Interoperability is a key to Industry 4.0. There are two possible trends to achieve this :
- A protectionist vision engages the company in a path of mostly internal control of knowledge.
- An expansionist vision uses the external means at the disposal of the company to achieve its goals.
These two opposing visions each have their strengths and weaknesses. I do not think there is a right or wrong approach, but it has to be consistent with the culture of the company and its leaders for it to be a success.
Interoperability can be done at the LEVEL of the ESM (Manufacturing Execution System) layer, or at the lower layer with traceability.
If the company chooses a single technology/supplier, it is easy to get a homogeneous layer but the risk of working with only one is big. So, you have to find your way for a system to ensure convergence and interoperability. This approach aims to be independent in terms of technologies.
Alexandre Langlais, CEO PERF’ACTOR
Then, thanks to actuators installed on the physical object, the digital twin can trigger and automate actions on the physical object : valve opening, light signals, various messages, etc. It also offers the ability to collaborate remotely and with several objects directly around the physical object. This makes it possible to optimize problem-solving but also to facilitate the training of the employees.
The 3D design also makes it possible to conduct virtual tours and facilitate remote monitoring.
Finally, compared to a simple preventive maintenance, predictive maintenance reveals the unique characteristics of an object. Because, even mass-produced, a product is never completely identical because of the multitude of elements that compose it and its various and varied conditions of use. Each physical object behaves in its own way. Digital twins take this uniqueness into account and help prevent or treat problems quickly.
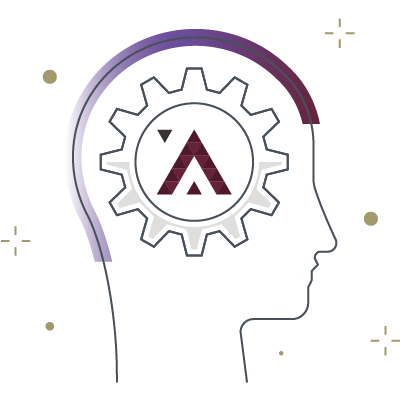
Feedback
When we analyze information from identical production machines, such as the vibration they emit, we notice significantly different results.
The behavior may not be visible easily, but the impact on lifespan and settings shows that it is necessary to go further in data analysis to find the right information that ensures the profitability of predictive maintenance. The data collected will then help to slow down the degradation of the machines.
Alexandre Langlais, CEO PERF’ACTOR
Costs, adaptation and risks
Setting up a digital twin can cost several thousand or even millions of euros, depending on the needs and the line of business. This also includes mastering new skills, new ways of working and new processes.
« But its cost is minimal compared to what it will bring to the company. » Pascal Naparty, Processia.
As we have seen above, the game is worth it because the digital twin has many advantages for the industry.
Also, some companies could miss out on a real competitive advantage in the long run, by ignoring this new technology.
Aside from the cost, the access to data by integrators may be of concern to some companies. Indeed, the majority of the companies that use digital twin installers allow them to access their data. We must therefore be vigilant on this point and analyse the current regulations.
We will have to make sure that we process the data collected as close as possible to its source. Deploying a Digital twin requires significant data storage and processing capacity. In order to be able to act quickly on possible failures and to maintain control over sensitive data, it would be wise to ensure the compatibility between the digital twin and the Edge computing.
« Nowadays, our digital twins rotate externally in computational centers, but we could imagine that they are embedded in the systems so that they self-monitor. In the event of critical decisions, this would avoid the latency required to send and return the data to the computing centers. And by keeping this data in one place, we would improve its security » Éric Bantegnie, ANSYS.
Digital twin: new opportunities to seize
The deployment of a digital twin can also be a way to diversify its business, or even to take the turn towards service and consulting. Thanks to predictive maintenance, companies are able to prevent outages and can offer a high value-added service to their customers. On the other hand, data analysis will help to support and inform strategic decision-making.
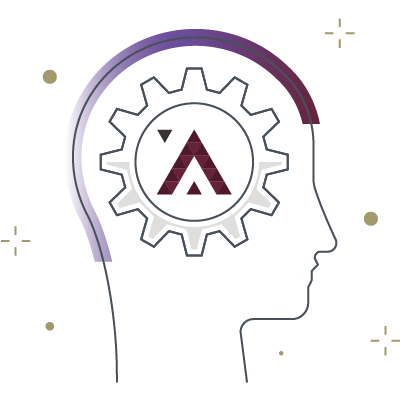
Feedback
Contracts with suppliers for the design of new machines or outsourced maintenance must be very clear about the limits of data ownership. Lawyers need to be attentive to this vision of information sharing.
Suppliers find an opportunity to provide new services and capture more value. However, the distribution must be done in a fair manner :
- The big contractors have sufficient clout to avoid these pitfalls, but innovation within their outsourcing ecosystem will be greatly reduced by preventing the development of new services that would allow them to gain a decisive advantage.
- The major and global suppliers of IOT secure their perimeter by imposing contracts and rules to the disadvantage of the smallest.
Alexandre Langlais, CEO PERF’ACTOR
This solution will also help to optimize and validate a technology. The information collected by the digital model allows us to anticipate possible failures and thus optimize the design and performance of a technology. It is also a way to develop the next generation of a product.
« It’s a simulation to visualize what happens if I change a particular parameter and, by comparison between the different scenarios, to get the best levers of optimization and the best action plan » Michel Morvan, Cosmo Tech.
Combining digital with physics, design with production and maintenance: digital twins have the role of combining these two worlds, creating synergies, breaking organizations into silos and generating new opportunities.
« The digital twin is spreading out, it will become a standard for the industry » Pascal Naparty, Processia.
In conclusion, the implementation of this solution represents an important shift for the companies. According to Gartner the digital twin is one of the top 10 strategic technology trends: two-thirds of companies with an IoT strategy are expected to implement this technology by 2022.
A Digital Twin project ?
✔ An expert of the industry of the future is listening to you for 45 minutes.✔ A 360-degree analysis to describe your level of maturity on 12 dimensions✔ Personalized advice to boost your competitiveness✔ Concrete cases adapted to your business✔ A visual and synthetic synthesis in your email inbox
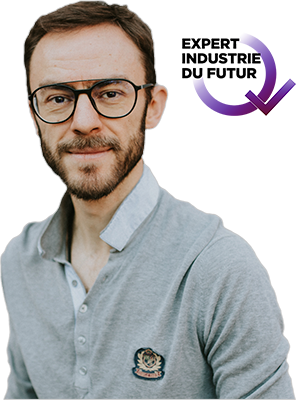
Alexandre Langlais, CEO PERF’ACTOR
Related topics that may interest you :
Industry 4.0 : a real challenge for leaders